Announced in 2008, Aston’s once-in-a-lifetime flagship redefines the expression ‘no expense spared’. With just a few cars to go before the magic ‘77’ have been produced, Classic Driver was given a tour of the model’s bespoke production facility at Gaydon and experienced the ‘£1.15m – plus local taxes – handover’.
This building is solely dedicated to the One-77. Spotlessly finished in white, the laboratory-like workshop is the perfect environment for assembling Aston’s most expensive road car yet. That’s not to say that working on the One-77 is a soulless occupation – far from it.
My guide for the day was the One-77 programme’s Chief Engineer, Chris Porritt, aided by the redoubtable Mark Gauntlett, spokesman for the company on all matters One-77.
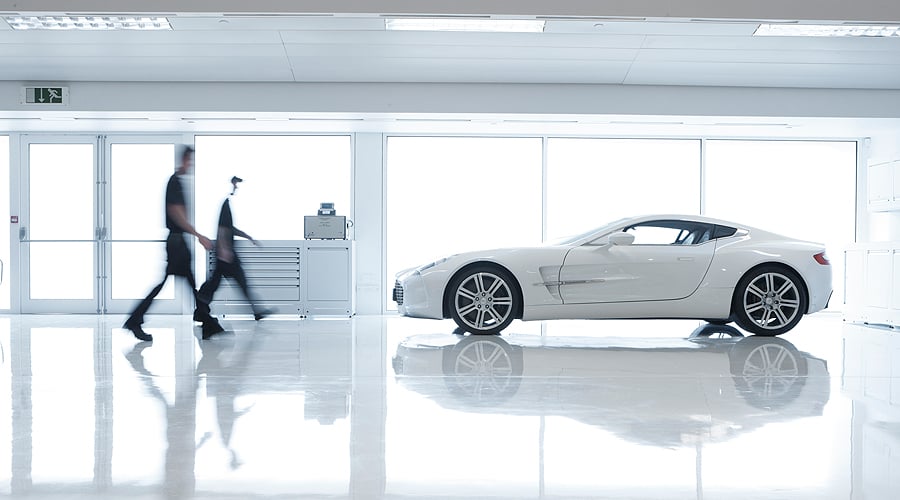


Both enthuse about the project, pointing out a detail here, a clever engineering solution there, that marks the whole project out as truly unique. And in the rarefied world of Aston Martin, that’s saying something.
As an example, one of the company’s standard production sports cars might take 200 hours to build. A One-77 needs 2,500 hours of skilled craftsmanship before the new owner can watch the flamboyant theatrical display that is the handover, and finally sit behind the wheel.
So many pieces are machined from a solid billet of aluminium alloy, titanium or high-grade steel, mere ‘mouldings’ are few and far between. The long, carefully sculpted transmission tunnel cover that will eventually be sheathed in leather is no common-or-garden stamping or extrusion: it’s formed by CNC precision milling. The light-switches, door-pulls, seat-belt surrounds set into the carbonfibre seats – virtually every part you can touch or see has been made especially for this car, including its slightly-larger-than-usual winged badge.


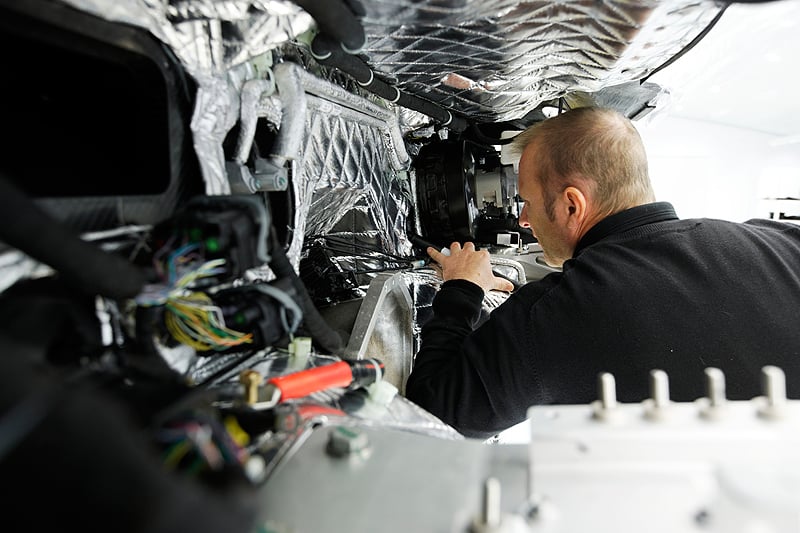
It’s known as an ‘A-class finish’. And that extends under the bonnet, behind the wheels or anywhere else that’s visible. The push-rod suspension at the rear has its own ‘window’ behind the seats. Up front, and with the bonnet raised, more of the all-carbonfibre chassis unfolds, with turned and anodised aluminium meeting exquisitely finished, high-gloss resin carbonfibre at Formula 1 levels of detailing and fit.
And it’s from Canadian motorsports supplier Multimatic that the Gaydon company sources the One-77’s carbonfibre chassis, with CPP of Coventry making the body panels and Cosworth of Northampton entrusted with developing Aston’s own 6.0-litre V12 into a lightweight, free-revving 7.3-litre motor producing in excess of 750bhp. “An extreme evolution” of the series-production engine is how Aston puts it.
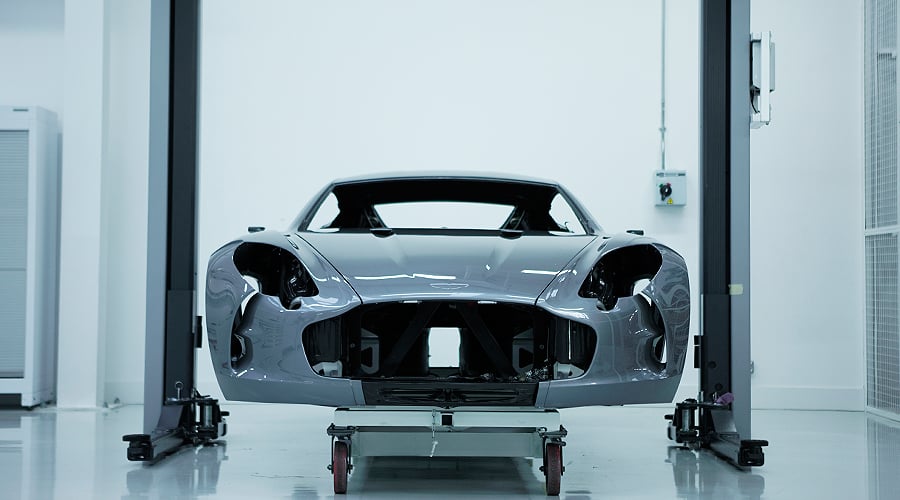

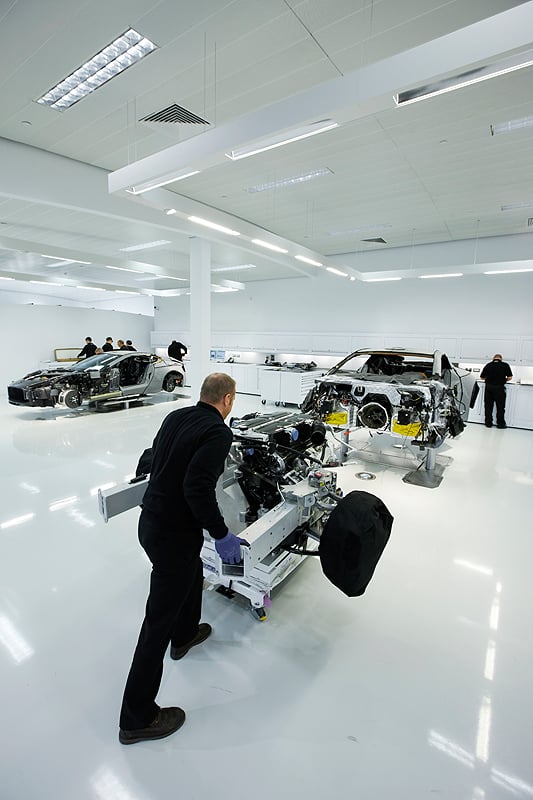
With the immensely tough chassis and lightweight composite parts stripped down, then painted and re-assembled in the main factory, it’s time for the car to be built up by hand in the One-77 building, where drivetrain, brakes, all plumbing, wiring and trim is carefully installed.
The rear-mounted gearbox, by the way, is a variation on the 6-speed robotised sequential manual transmission, the ‘Sportshift’, used in Aston’s series production cars. V8 Vantage owners, please be reassured: it’s tough.
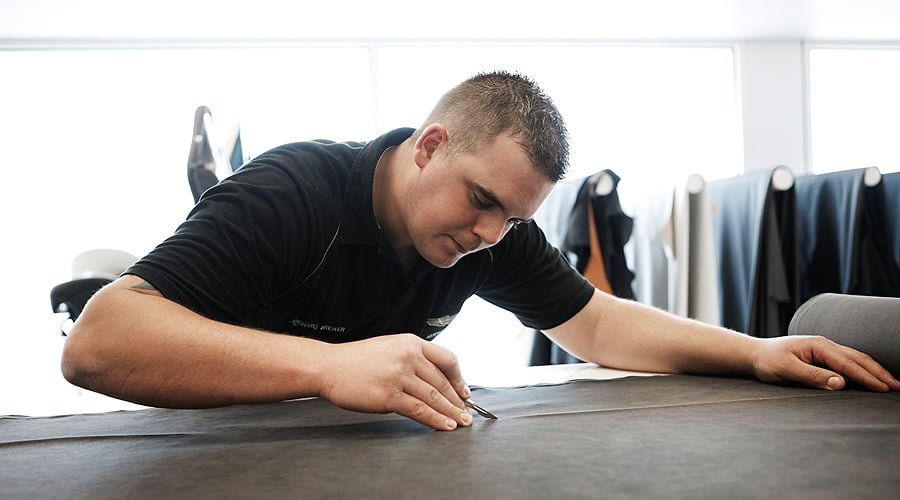
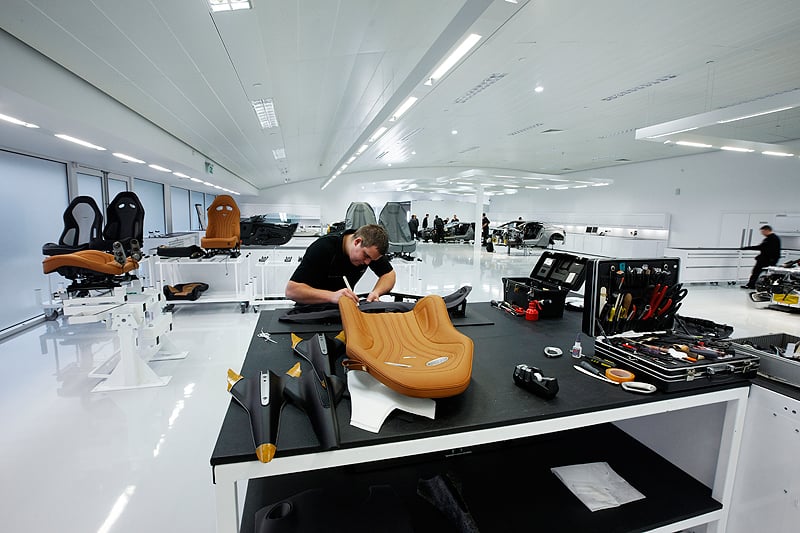
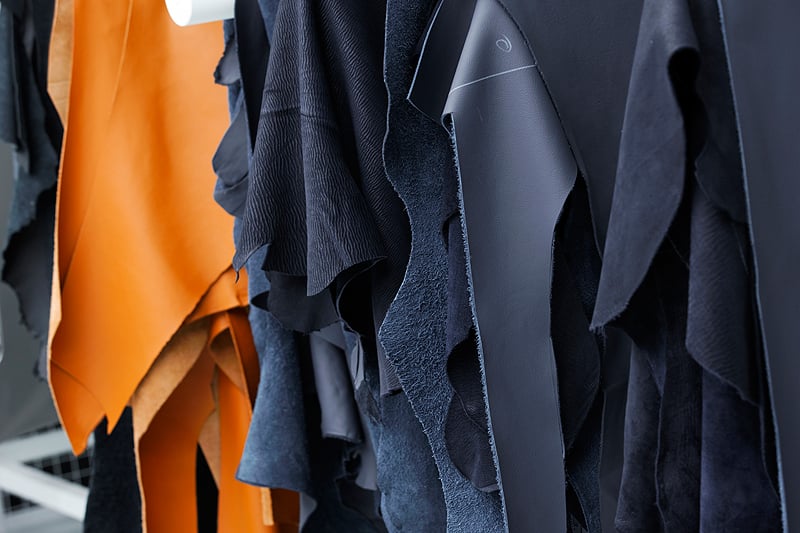
As you’d expect, each individual chassis can be painted and trimmed to suit an owner’s tastes. One-77 has its own range of colours (such as ‘Black Pearl’) but the potential palette inside and out is infinite. All customers will have visited Gaydon at least once in order to settle on a final configuration. And that can go right down to whether the handmade grille has polished or satin edges…
(As an example, the grille alone takes 1.5 weeks to fabricate, with all parts cut and finished by hand. And One-77 has unique-to-the-car B & O speakers in the doors, delicately sculpted from solid. I could go on.)
Available in LHD and RHD, more than 55 cars have been delivered so far and, with the start of V12 Zagato production in the same facility next spring, potential buyers might be advised to consider one of the last remaining production slots.
While members of the press have yet to drive a One-77, many owners are enjoying their new acquisitions. One has covered some 22,000 kilometres in just nine months and it’s interesting to note that the very special car can be serviced by all authorised Aston Martin agents. It’s also been designed with a degree of usability to add to its colossal performance: a 300-mile (500km) range should be on one tank of fuel. Porritt has driven the car back from testing in Italy, two-up with soft luggage for an overnight stop-over.
Putting the not inconsiderable revenue issues aside, the project came about principally because the company ‘could’, stretching the design and engineering team’s skills and creativity.
I’ve seen many One-77s over the past year or so but, in the calm, uncluttered environment at Gaydon, the model takes on a new persona. Marek Reichman (above) and his team have done a terrific job. It’s such a clever design with the ‘power bulge’ that’s actually formed by two sculpted valleys in the bonnet, the fan-like array of curved stainless steel bonnet louvres, the extravagant engine air-exit and long side-strake and so much more.
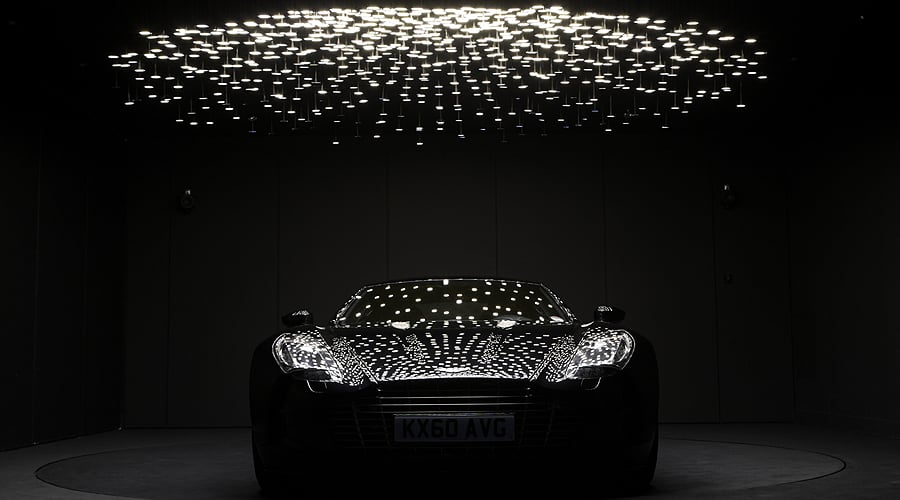
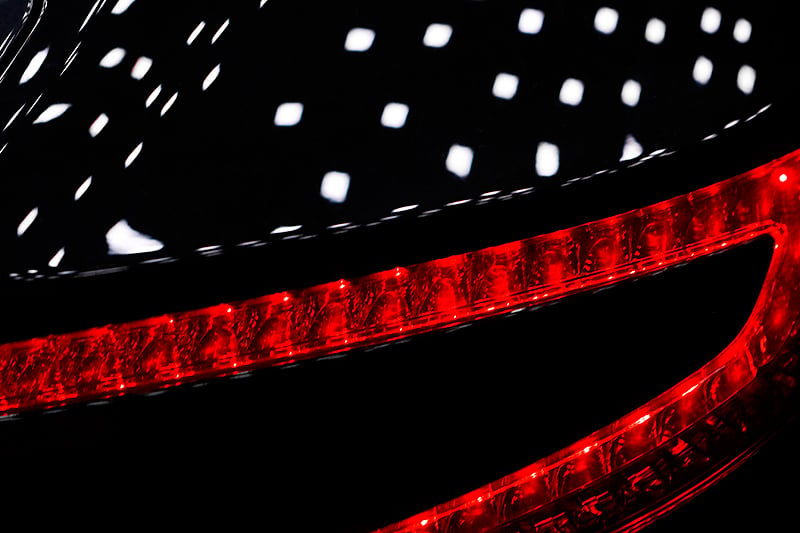
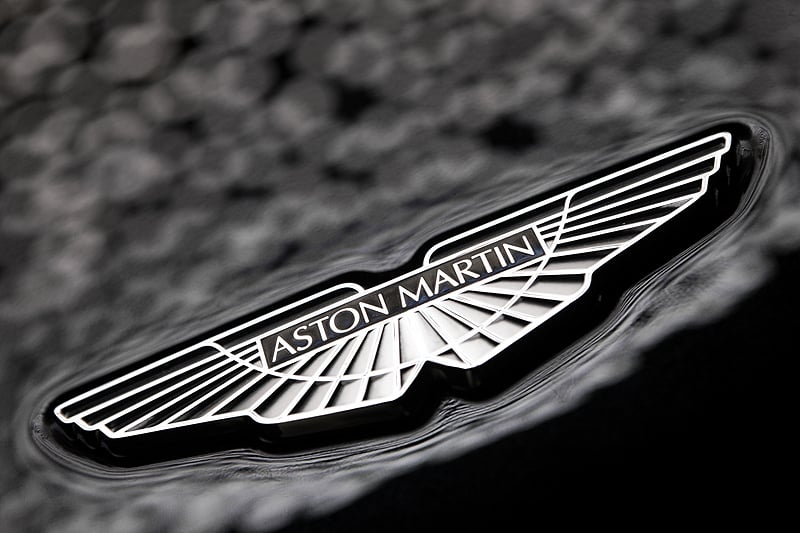
All of this becomes apparent as, finally, the lights are dimmed and you are invited to relax on a leather sofa and experience the ultimate handover. We are in the discreetly furnished reception area for One-77 clients and That Time has come.
With Bang & Olufsen surround-sound swirling, steadily pulsing lights in a hitherto unlit room flash brighter and faster, a shape becomes ever more apparent behind smoked glass doors. It is YOUR One-77 and it’s ready for collection.
As an experience, that alone is stunning. And it’s one that quite perfectly matches the state-of-the-art, brilliantly styled and executed Aston Martin One-77.
Text: Steve Wakefield
Photos: Aston Martin